Soldadura MIG: qué hay que tener en cuenta
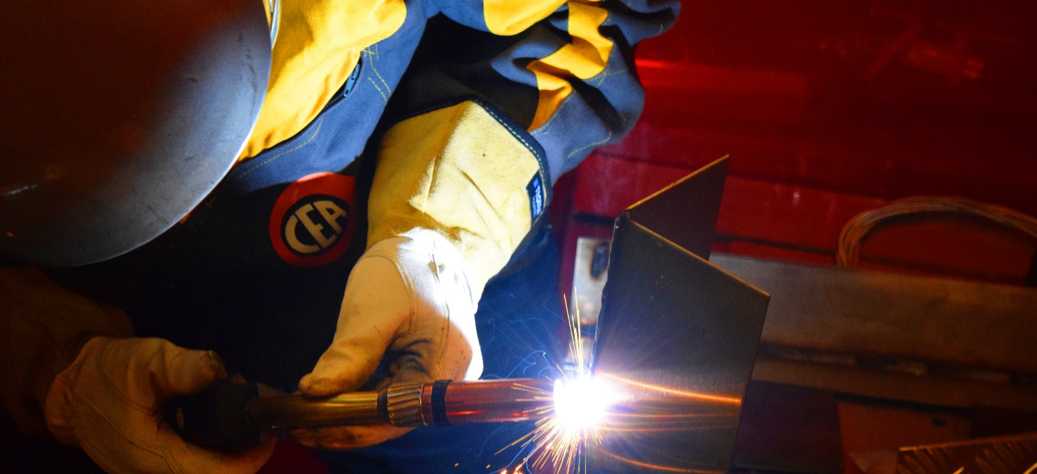
Empecemos por lo que significa soldadura MIG. MIG significa Metal-arc Inert Gas (gas inerte de arco metálico). Por el nombre está claro que esteproceso de soldadura utiliza un arco eléctrico, que surge directamente del metal de aportación, y el gas inerte para proteger el baño de soldadura de la oxidación.
Este proceso forma parte de la soldadura con alimentación por hilo y permite alcanzar una productividad excelente.
La antorcha de soldadura alimenta tanto el hilo, por el que pasa la corriente que genera el calor necesario para soldar, como el gas inerte, que protege el baño y evita la formación de escoria a medida que se crea el cordón.
Para conseguir una soldadura fuerte y sin inclusiones, debemos prestar atención a:
- El aporte de calor
- La velocidad en relación con la corriente y la tensión
- El gas inerte
Lea nuestro eBook sobre la evolución del proceso de soldadura
Problemas de la soldadura MIG: aporte de calor
El elevado aporte de calor generado por este tipo de soldadura puede crear grietas calientes que deben corregirse para no comprometer la estanqueidad global del cordón.
Una temperatura insuficiente también puede dar lugar a problemas debido a la falta de uniformidad de la soldadura y, por tanto, a una penetración deficiente.
Tensión, corriente y velocidad para una soldadura impecable
Antes de empezar a soldar, es necesario ajustar todos los parámetros del generador para disponer de una configuración adecuada al tipo de trabajo, ya que el aumento de la tensión y la corriente se traduce en un aumento de la temperatura del baño de soldadura. En efecto, en el caso de temperaturas muy elevadas, la necesidad de un enfriamiento rápido y eficaz aumenta considerablemente.
Vamos a explicarlo todo mediante una fórmula con los siguientes parámetros
- H aporte de calor, es decir, la energía del baño de soldadura
- η eficacia de la transferencia de calor
- V tensión del arco en voltios
- I corriente en amperios
- v velocidad de avance
Si examinamos la fórmula de la soldadura por arco H= η VI/v, queda claro que, al aumentar la velocidad de avance, disminuye el aporte de calor.
Por lo tanto, cuanto más experto sea el soldador, más rápido avanzará cuando sea necesario. Si añadimos una máquina avanzada en términos de software para ayudarle, la soldadura será de alta calidad.
Defectos debidos al gas
Además de utilizar un gas adecuado para el tipo de soldadura, es muy importante vigilar la cantidad de gas que sale de la antorcha para que la soldadura esté siempre protegida.
Si no sale suficiente gas, el oxígeno puede llegar al baño de soldadura y provocar porosidad.
La oxidación también puede producirse cuando se aumenta demasiado el flujo de gas inerte, generando turbulencias que incluyen aire en lugar de mantenerlo alejado de la soldadura.
Para evitar los defectos típicos de este tipo de soldadura y aumentar la eficacia, se han desarrollado tecnologías que controlan digitalmente los ajustes de la soldadura MIG que hemos comentado hasta ahora.
LEER TAMBIÉN: "Por qué elegir fabricantes italianos de máquinas de soldar"
Las ventajas de la soldadura MIG de arco pulsado
El proceso de soldadura con control digital de la corriente pulsada proporciona ventajas significativas.
Los modernos generadores para soldadura MIG/MAG permiten seleccionar diferentes formas de onda, que garantizan una transferencia uniforme del metal y una penetración perfecta.
Simplificando el proceso de transferencia del arco pulsado, podemos imaginarlo funcionando a través de una corriente de base, que fluye del hilo a la pieza, de intensidad suficiente para generar y mantener el arco, seguida de un pico que hace que se desprenda la gota.
La penetración del depósito viene determinada por la corriente de pico, mientras que el aporte térmico del baño de soldadura está relacionado con el valor de la corriente eficaz.
Los generadores inverter de última generación disponen de una pantalla en la que es posible seleccionar varias formas de onda, en función del trabajo a realizar.
La versatilidad y facilidad de uso de estas soldadoras MIG digitales es evidente ya que, con un rápido vistazo a la pantalla, el soldador puede guiarse en el ajuste de todos los parámetros.
Al utilizar máquinas con software de vanguardia, el trabajo es más rápido y los cordones de soldadura son estética y funcionalmente mejores.
LEA TAMBIÉN: "5 buenas razones para comprar máquinas de soldar de alta tecnología "
Problemas y soluciones para la soldadura MIG
Como hemos mencionado, la soldadura MIG es ideal cuando queremos trabajar más rápido manteniendo un alto estándar de calidad; si además utilizamos corriente pulsada, las ventajas son aún mayores.
La soldadura MIG de corriente pulsada se utiliza en chapas finas, aleaciones ligeras y aleaciones no ferrosas, acero inoxidable y aluminio.
Este método de soldadura en particular resuelve una serie de problemas, como las inclusiones en el cordón debidas a una corriente mal gestionada y las quemaduras en la chapa por exceso de calor.
Nuevas tecnologías y procesos de soldadura especiales
La evolución del proceso de soldadura MIG ha llevado hoy a los fabricantes a crear soluciones específicas para facilitar algunos tipos de tratamiento especialmente complejos.
La digitalización de los parámetros y el estudio de los problemas habituales de los soldadores han dado lugar a programas para procesos especiales que garantizan las siguientes ventajas:
- Estabilidad del arco
- Bajo aporte de calor
- Soldadura rápida
- Soldadura con alta penetración (especialmente en aceros de espesor medio/alto)
- Soldadura vertical ascendente
Otros beneficios tangibles vienen dados por la posibilidad de automatizar los sistemas de soldadura, parcial o totalmente, utilizando maquinaria que trabaje con el operario humano o gestione totalmente un robot.
Dada la revolución que está experimentando la industria en los últimos años, disponer de maquinaria que ayude a aumentar la eficiencia de los trabajadores es esencial.
Tener la oportunidad de integrar modernas tecnologías de automatización con maquinaria que ya se encuentra en la empresa, lo que se conoce como retrofitting, brinda la oportunidad de afrontar la industria 4.0 evitando grandes inversiones.
{{cta('5535a6eb-336c-4063-9586-0c8e74209929','justifycenter')}}