The progress of welding process
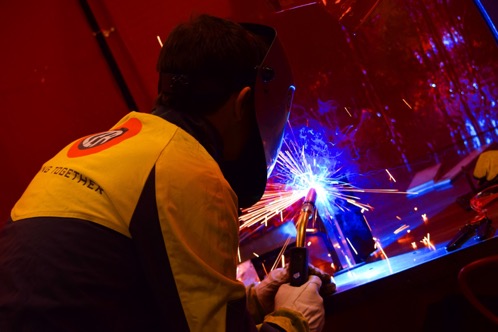
Like all the technologies used in industry, even the welding process has undergone significant developments over the years.
To melt metal and subsequently achieve a joint, it is necessary to apply large amounts of heat, but what is important is controlling the heat input of the weld pool.Going from welding machines that used a flame to ones using an electric arc, and later to the digital control of current generators, the world of welding is in constant development.
Welding process: Oxyacetylene welding
When discussing old welding methods, it’s appropriate to start with oxyacetylene welding, which was born over a century ago.
Oxyacetylene welding does not use electricity to raise the temperature to the melting point, rather it employs the combustion of acetylene and oxygen.
This type of process uses a filler material, commonly called the stick, which is melted by the flame directly over the joint to weld.
The type of welding in question could have defects such as lack of penetration, which takes place when the welding is not done at a high enough temperature, or stuck welds, i.e. the formation of oxides.
The metals that can be welded with this technology are: cast iron, carbon and stainless steel, aluminium, copper.
Over time, oxyacetylene welding has been replaced with arc welding systems.
Electricity in the development of the welding process
In the 20th century, the welding process underwent the greatest revolutions thanks to the use of electricity.
Arc welding began to take hold, while welding with a coated electrode was one of the most widely used until the early 2000s.
At first, the problems in the welding process with electrode were due to the lack of coating on the electrode itself, which generated oxidations and inclusions. Protecting the electrode using a coating with a deoxidizing material solved this major complication.
The disadvantages due to the presence of slag and porosity in the weld gave way to a further technological change with TIG and submerged arc welding.
TIG welding and MIG / MAG welding
These processes solve some of the main welding problems. Both TIG welding and MIG/MAG welding use gas to protect the weld pool from oxidation.
TIG welding uses a torch with a non-consumable tungsten electrode from which springs the electric arc that melts the metal. The weld pool is shielded by a jet of inert gas, usually Argon or Helium, that keeps away oxygen and the resulting defects.
This type of welding can be done with or without filler material.
TIG welding machines are widely used in industry, as they ensure high quality work, but they must be used by specialised workers with excellent technical skills.
MIG and MAG welding differ only by the type of gas each uses: in the former, protection is provided by an inert gas (usually Argon), whereas the latter uses a mixture of inert and oxidizing gas (Oxygen or Carbon Dioxide).
These processes are the evolution of submerged arc welding and they use wire feed as well, which plays the dual role of electrode and filler material.
MIG/MAG welding machines enable speeding up the process, obtaining good quality beads.
Today’s welding machines: inverters and digital controls
Inverter technology has been a true revolution in the welding sector. The use of this component, to replace traditional transformers, has enabled welding with a direct current, obtaining cleaner and more precise welds with a significant reduction in fuel consumption.
Another advantage in MIG welding and TIG welding attributable to inverter generators, is that considerable power can be obtained with small machinery, which is therefore easier to transport.
Additionally, being able to use digital welding machines today, that help the operator select the ideal settings, is a further technological development that, along with industrial robotics, has solved many issues due to inaccurate human action.
{{cta('5535a6eb-336c-4063-9586-0c8e74209929')}}